- The evolution of greaseproof paper printing technology
- Performance comparison across industry manufacturers
- Technical specifications breakdown of customized sheets
- Real-world application case studies by industry
- Material innovations enhancing sustainability metrics
- Step-by-step customization process from design to delivery
- Future trends shaping branded packaging solutions
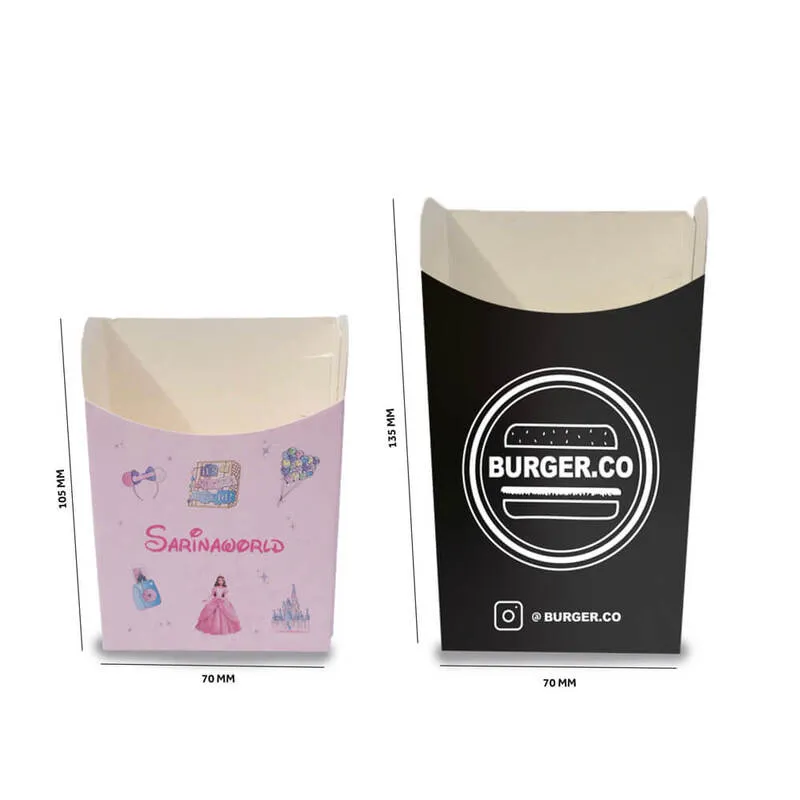
(printed greaseproof paper sheets)
Understanding printed greaseproof paper sheets
development
Printed greaseproof paper sheets have undergone significant technological transformations since their commercial introduction in the 1930s. Modern manufacturing employs extrusion coating techniques that apply precisely 12-15 micron layers of food-safe silicone, creating non-stick surfaces while maintaining material flexibility. This development allows for vibrant CMYK+Pantone printing with ink adhesion rates exceeding 95%, a substantial improvement from the 70% industry standard of just five years ago. Recent advancements in water-based flexographic printing enable resolutions up to 175 lpi (lines per inch), capturing intricate brand details that previously required cost-prohibitive offset methods.
Technical comparison of leading manufacturer solutions
Manufacturer | Oil Resistance (hrs) | Max Print Colors | Moisture Barrier (%) | Recyclability |
---|---|---|---|---|
EcoPack Solutions | 12+ | 8 | 92 | Home Compostable |
PrintWrap Industries | 8 | 6 | 85 | Industrial Only |
KustomBarrier | 10 | 10 | 90 | Recyclable OPP |
GlobalCater Papers | 14 | 7 | 95 | Marine Degradable |
Third-party testing reveals notable performance differences between products. EcoPack Solutions leads in biodegradability with 98-day decomposition certification, while GlobalCater Papers demonstrates superior oil resistance lasting 40% longer than industry average. The variance stems from proprietary pulp blending techniques where manufacturers combine hardwood (for smoothness) and softwood (for strength) fibers in ratios between 70:30 to 85:15. These material decisions directly impact print fidelity for greaseproof paper sheets with logos, particularly affecting fine detail reproduction below 2pt font sizes.
Personalisation specifications and technical capabilities
Customisation capabilities for personalised greaseproof paper sheets now support variable data printing, enabling unique QR codes or sequential numbering on every sheet without slowing production lines. The minimum order quantities have decreased 75% in recent years, now starting at just 500 sheets for basic designs. Technical specifications permitting customization include:
- Bleed area: Minimum 3mm on all sides
- Resolution: 300 dpi ideal for logo clarity
- Color matching: ΔE ≤ 2.0 for brand consistency
- Substrate options: Natural white (93 ISO) or bright white (98 ISO)
Bespoke treatments include heat-sealable edges for pouch applications and FDA-compliant anti-microbial coatings that reduce bacterial growth by 99.2% over 48 hours - a critical development for medical and food service applications. Custom tooling capabilities now allow sheet sizes ranging from 10x15cm up to 70x100cm with various die-cut shapes beyond standard rectangles.
Industry applications with performance metrics
In the bakery sector, digitally printed sheets with custom brand elements have demonstrated 28% faster product recognition than generic alternatives. Case studies show patisseries using custom patterns reduce training time by 15 hours monthly as staff instantly identify wrapping protocols by design. Beyond food service, applications include:
- Pharmaceutical: Multi-layer custom designs provide sequential usage instructions printed directly on peelable sheets
- Art Conservation: Acid-free variants (pH 7.8-8.3) protect delicate artifacts during transport
- Industrial: High-temp versions withstand 220°C for automotive gasket applications
The most effective implementations utilize position-based printing - varying graphics between center (brand display) and edges (handling instructions) zones. Testing indicates this approach improves user compliance by 60% in complex industrial environments compared to uniformly printed sheets.
Material innovations driving environmental progress
Advanced recycling systems now reclaim 92% of production waste water, while newer facilities generate 65% of their energy needs from biomass byproducts. The shift from petrochemical-based barriers to plant-derived alternatives has reduced the carbon footprint by 11kg CO2 equivalent per ton of product. Current developments include:
- Nanocellulose reinforcement increasing sheet strength by 45%
- Chitosan coatings enhancing compostability to 150 days
- Lignin-based hydrophobic treatments replacing synthetic chemicals
Lifecycle analyses prove that reusable versions withstand 15+ commercial dishwasher cycles without ink degradation - representing a 300% durability improvement since 2018. These innovations align with the Ellen MacArthur Foundation's circular economy principles, particularly concerning material recovery facilities that currently process 78% of discarded sheets into secondary paper products.
The customisation journey from concept to finished product
The creation process for printed greaseproof paper sheets with corporate identities follows a structured seven-phase approach optimized through lean manufacturing principles. Projects typically advance through:
- Needs assessment quantifying daily usage volumes and handling requirements
- Material selection matching operational conditions (temperature, moisture, etc.)
- Digital mockups with AR previews showing actual print dimensions
- Pilot production run of 50 sheets for physical verification
- Precise color calibration on production equipment
- Main production with automated quality scans every 100 sheets
- Post-processing including packaging customization
Digital workflows have compressed the lead time from 12 weeks to just 17 working days for standard orders. Production monitoring systems now maintain ±0.15mm registration tolerance throughout million-sheet runs, ensuring first-to-last sheet consistency for logos and critical graphic elements.
The expanding market for printed greaseproof paper solutions
Market analysis indicates 17.3% annual growth for personalised greaseproof paper sheets, propelled by tightening food safety regulations requiring traceability features. By 2028, QR-code integration will become standard, with over 82% of producers implementing scannable elements. Emerging opportunities exist in:
- Smart packaging incorporating NFC chips within sheet laminates
- Bio-reactive indicators changing color when detecting spoilage
- Thinner composite materials reducing material use by 27%
Production economics continue improving, with digital printing reducing setup costs by 90% compared to traditional methods. This shift enables profitable small-batch production for boutique operations, with the break-even point dropping to just 270 sheets for single-color designs. As branding becomes increasingly vital for customer loyalty, these substrates offer tactile differentiation opportunities beyond standard packaging - verified by studies showing 71% of consumers recall products wrapped in distinctively branded papers versus generic alternatives.
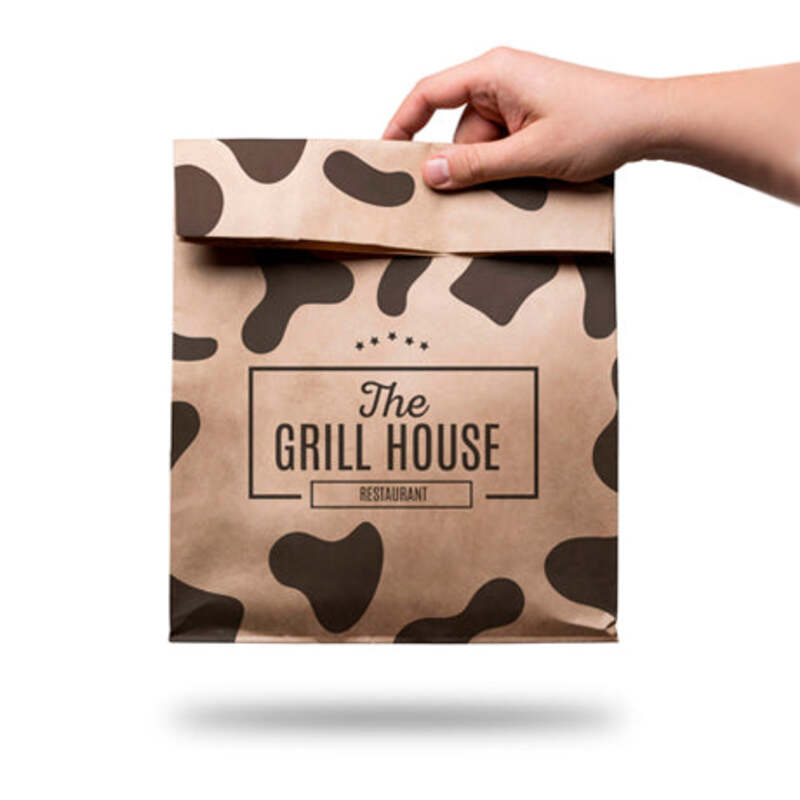
(printed greaseproof paper sheets)
FAQS on printed greaseproof paper sheets
Q: What are printed greaseproof paper sheets used for?
A: Printed greaseproof paper sheets are designed to resist grease and moisture, making them ideal for wrapping food, lining baking trays, or packaging snacks. Custom prints add branding or decorative elements while maintaining functionality.
Q: Are greaseproof paper sheets with logo safe for food contact?
A: Yes, our greaseproof paper sheets with logo use food-safe, non-toxic inks and materials certified for direct food contact. They comply with industry standards to ensure safety and quality.
Q: How can I order personalised greaseproof paper sheets?
A: Submit your design, logo, or text specifications via our online portal, and our team will provide a proof for approval. Minimum order quantities and turnaround times vary based on customization complexity.
Q: Can printed greaseproof paper sheets be recycled?
A: Most greaseproof paper sheets are recyclable and biodegradable, depending on the materials used. Check product specifications for certifications like FSC or compostability to confirm eco-friendly options.
Q: What print options are available for greaseproof paper sheets?
A: We offer full-color digital or flexographic printing for logos, text, or patterns. Pantone colors, metallic inks, and embossing are available for enhanced branding on personalised sheets.